Preicison Plastic Injection Molding
-
Custom Thermoplastic Injection Molding capabilities
-
A fully automated production workshop with 3 injection molding centers
-
Short, Medium, and Large size Injection Molding Production Runs
-
Process Most Engineering and Commodity Grade Resins
-
One special injection room for producing optical lenses, guides, and fresnel products
-
Custom Automation/ medical/Security system Engineering and Manufacturing
-
Custom Inventory Programs
Types of Injection Molding Technologies We Offer

Plastic Injection Molding
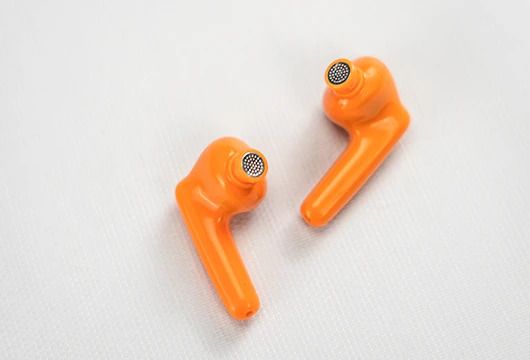
Two-Color Injection Molding
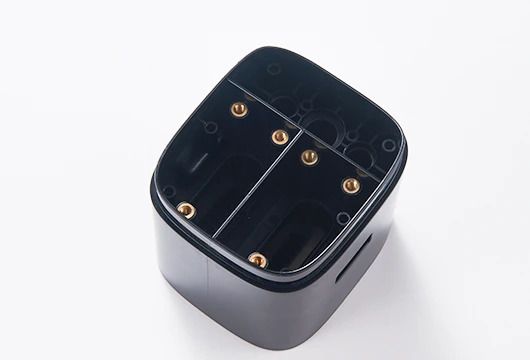
Insert Molding
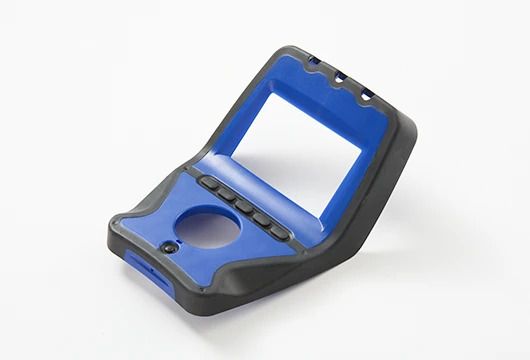
Overmolding
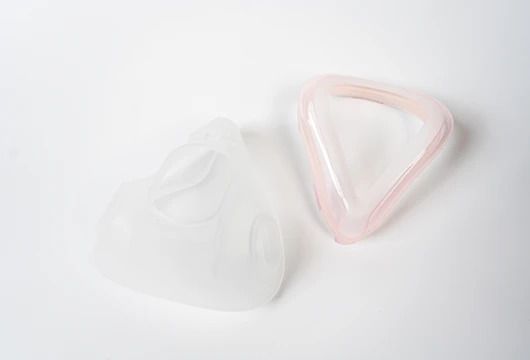
Silicone Injection Molding
Custom Injection Molding Solutions
Jinnfeng Plastic provides a one-stop solution for customized precision plastic injection molding, including free injection molding quotes, professional design for manufacturability (DFM) analysis, rapid prototyping, mass production, and process improvement suggestions. Through optimized design and strict quality management, we ensure efficient production and excellent performance of finished injection molded products. For customized solutions or more information, please feel free to contact us!
Rapid Prototyping
Low Volume Production
Injection Molding Materials
There are over 200 common injection molding materials. It includes general-purpose plastics, engineering plastics, and high-performance materials. Modified materials are optimized from base materials by adding fibers, flame retardants, or adjusting molecular structures. Globally, there are over 18,000 commercial modified materials to meet performance requirements in different scenarios.
Injection Molding Material Selection Principles for Product Designers
-
Select material properties based on functional needs: High-temperature resistance(PC, PEEK), Impact resistance(ABS), Transparency(PC, PMMA), Lightweight(PP)
-
Consider processing parameters such as fluidity and shrinkage rate to ensure molding precision.
-
Prioritize cost-effective and recyclable materials. For regulated industries (e.g., medical, food), use certified food-grade or biodegradable materials.
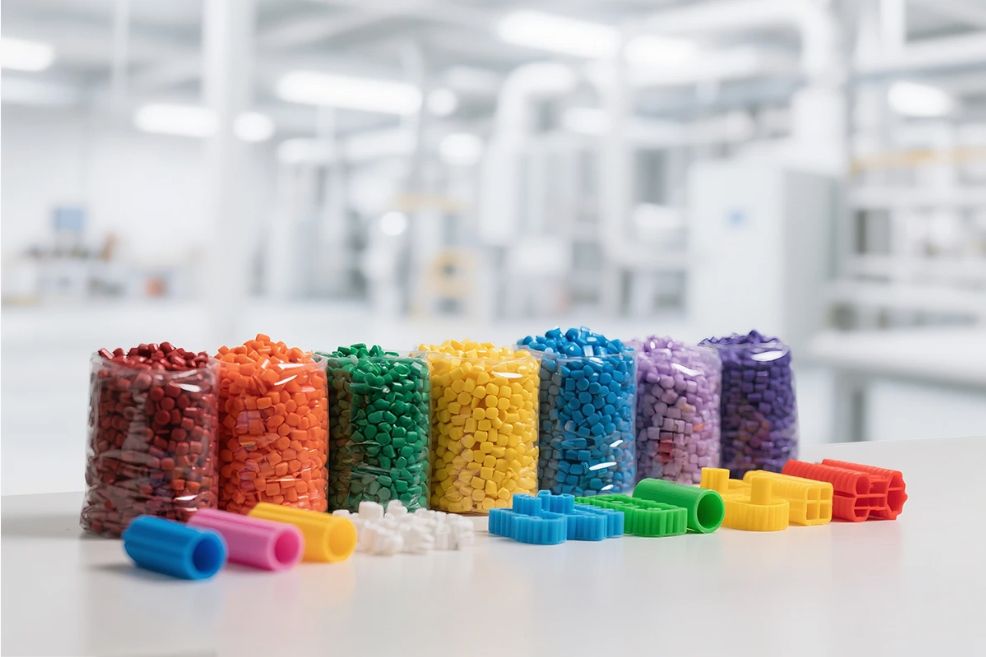
Custom Surface Finishing for Injection Molded Parts
Beyond functional performance, the right surface finish elevates your product's aesthetics and durability. At Jinnfeng Plastic, we combine in-house standard finishing techniques with a 15+ year network of specialized suppliers to deliver textures, colors, and coatings that align with your brand vision. Whether your parts are molded in China facility, you won't be disappointed.
In-House Surface Finishing Solutions
Standard Finish (SPI Class A/B)
-
Mold-Textured Surfaces: VDI 3400 standards (e.g., fine grain, leather patterns).
-
Polishing & Gloss Control: Achieve Ra 0.05μm mirror finishes or matte effects.
-
Sandblasting: Uniform roughness (Ra 1.6-3.2μm) for paint adhesion or grip enhancement.
Decorating Techniques
-
Pad Printing: Durable logos/text on curved surfaces (medical devices, tool grips).
-
Laser Engraving: Permanent markings for serial numbers, certifications (UL, ISO).
Partner-Enhanced Specialty Finishes
Functional Coatings
-
EMI/RFI Shielding: Conductive nickel coatings for electronics enclosures.
-
Anti-Fingerprint (AF) & UV-Resistant Layers: Protects consumer device surfaces.
Aesthetic Treatments
-
Electroplating: Chrome, nickel, or gold finishes for automotive trims.
-
Anodizing (Metal Inserts): Color-stable aluminum components.
Steps for Precision Plastic Injection Molding
Requirement Analysis and Design Communication
Requirement analysis and design communication are crucial steps in ensuring the success of customized mold opening and injection molding. Effective communication ensures that all parties involved in the project (clients, designers, engineers, mold manufacturers, etc.) have a clear and consistent understanding of the requirements and design plan.
Requirement Analysis and Design Communication
Requirement analysis and design communication are crucial steps in ensuring the success of customized mold opening and injection molding. Effective communication ensures that all parties involved in the project (clients, designers, engineers, mold manufacturers, etc.) have a clear and consistent understanding of the requirements and design plan.
Requirement Analysis and Design Communication
Requirement analysis and design communication are crucial steps in ensuring the success of customized mold opening and injection molding. Effective communication ensures that all parties involved in the project (clients, designers, engineers, mold manufacturers, etc.) have a clear and consistent understanding of the requirements and design plan.
Requirement Analysis and Design Communication
Requirement analysis and design communication are crucial steps in ensuring the success of customized mold opening and injection molding. Effective communication ensures that all parties involved in the project (clients, designers, engineers, mold manufacturers, etc.) have a clear and consistent understanding of the requirements and design plan.
Requirement Analysis and Design Communication
Requirement analysis and design communication are crucial steps in ensuring the success of customized mold opening and injection molding. Effective communication ensures that all parties involved in the project (clients, designers, engineers, mold manufacturers, etc.) have a clear and consistent understanding of the requirements and design plan.
Requirement Analysis and Design Communication
Requirement analysis and design communication are crucial steps in ensuring the success of customized mold opening and injection molding. Effective communication ensures that all parties involved in the project (clients, designers, engineers, mold manufacturers, etc.) have a clear and consistent understanding of the requirements and design plan.
Our Strength of Precision Plastic Injection Molding
Injection Molding Cases
Quality Assurance
The Jinnfeng Plastic design, engineering, and manufacturing teams behind your project are also behind your vision, enhancing your ideas and bringing them to life. It takes years of experience to build the kind of expertise we can offer in engineering and manufacturing services which is why we have successfully serviced large customers and global industry leaders.
Thanks to our highly vetted supplier network and ISO 9001-certified Quality Management System, it’s always possible to have your parts manufactured with industry-specific certifications. Our manufacturing partner network can certify to the following standards: ISO 14001:2015, IATF 16949:2016, ISO 13485:2016 and ISO 9001:2015.
Industry Applications
Our areas of expertise include: precision injection molding, medical injection molding, tungsten steel part processing, and injection molding production of special plastics such as PEEK, LCP, PEI, PPS, PPSU, PFA, etc. The company is certified to ISO9001, ISO14001, ISO/IATF16949, and ISO13485 medical system standards. Over the years, with excellent quality, delivery, and service, we have earned the trust of customers both domestically and internationally, becoming a key partner for many international large-scale enterprises in various fields, including automotive engineering, electronic and electrical engineering, aerospace, medical technology, tooling fixtures, and machinery equipment manufacturing.
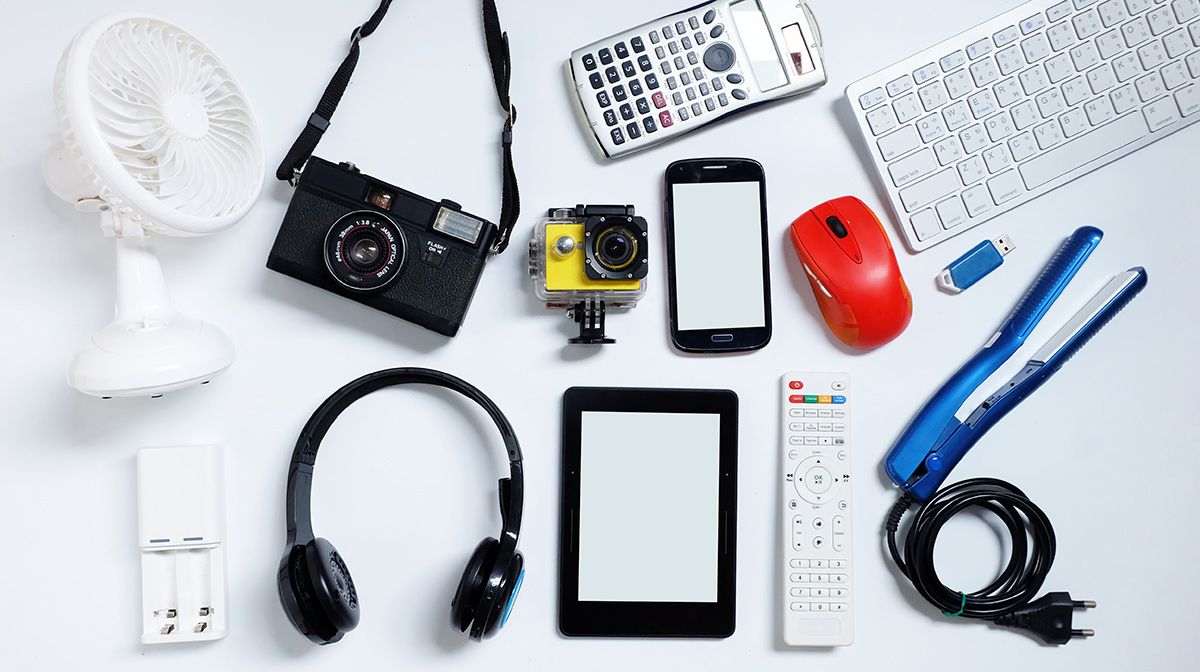
Consumer Electronics Precision Parts Solutions
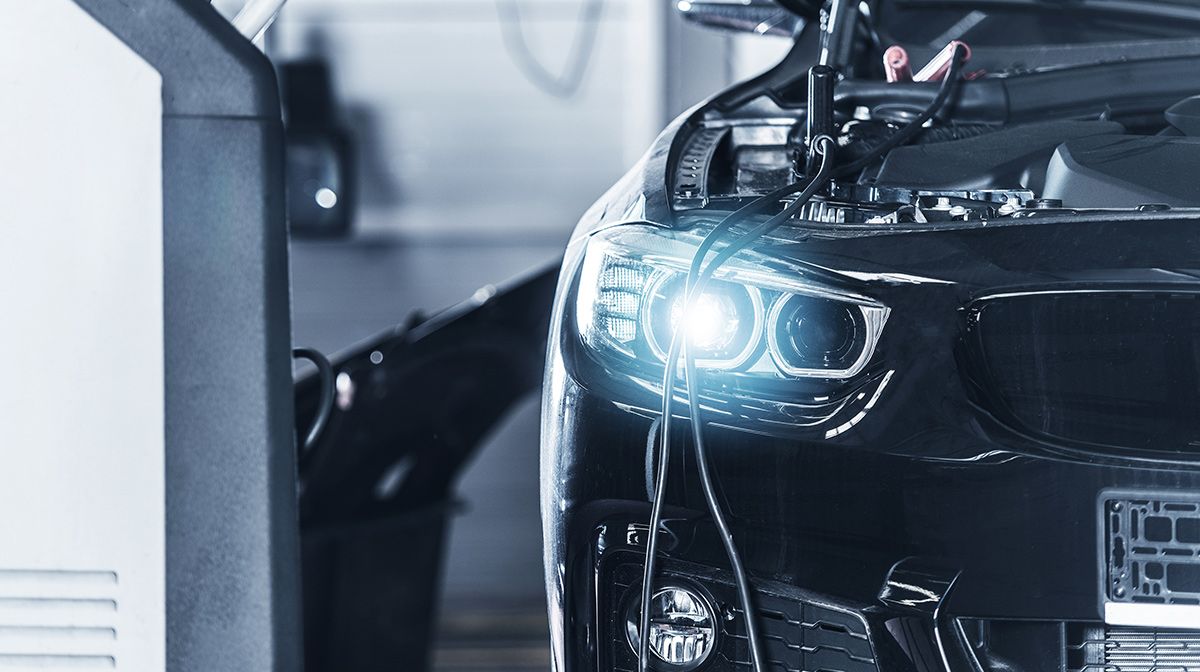
Automotive Injection Molding Components Solution
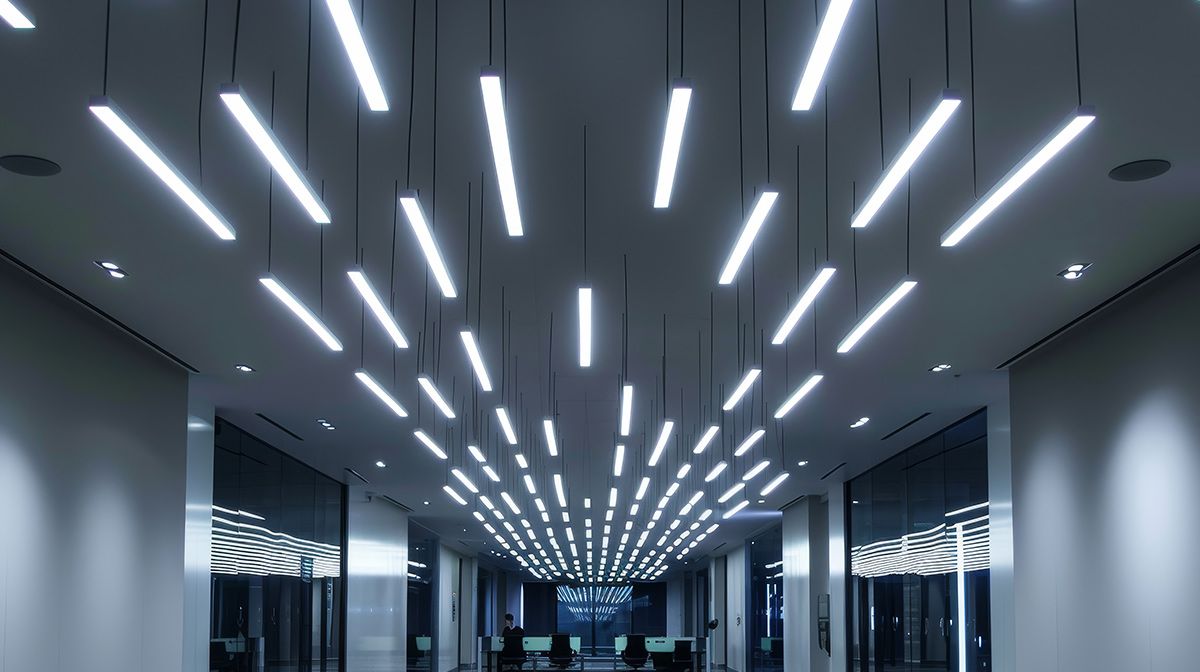
LED Lighting injection mold components Solution
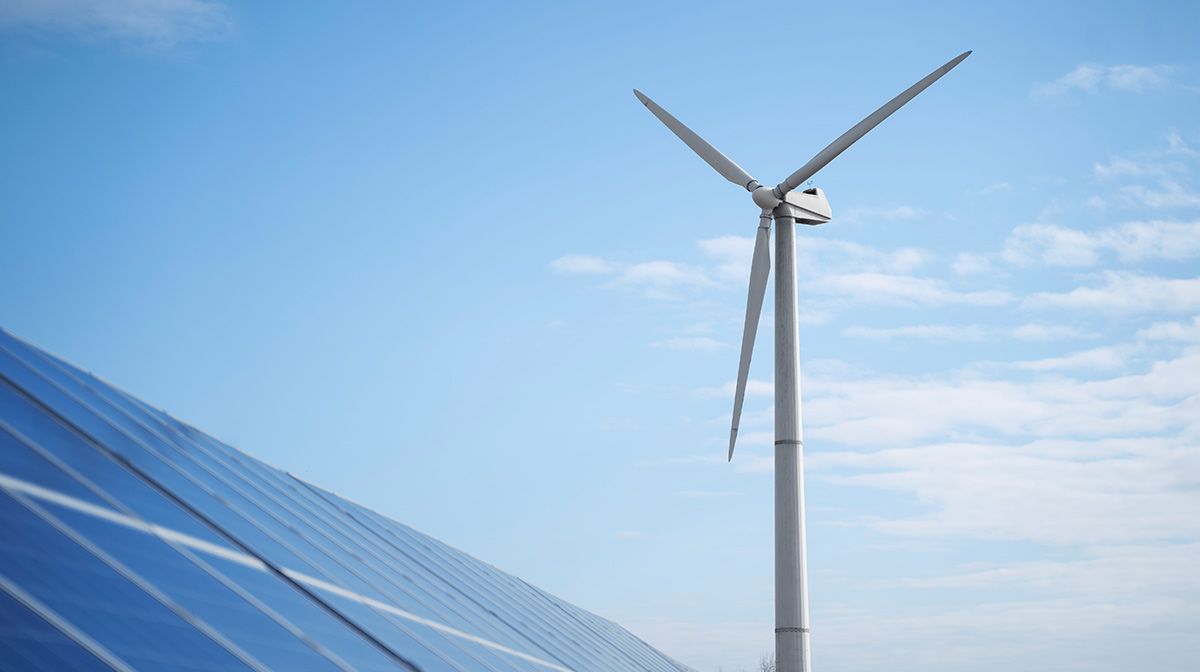
Energy & Environmental injection mold components Solution
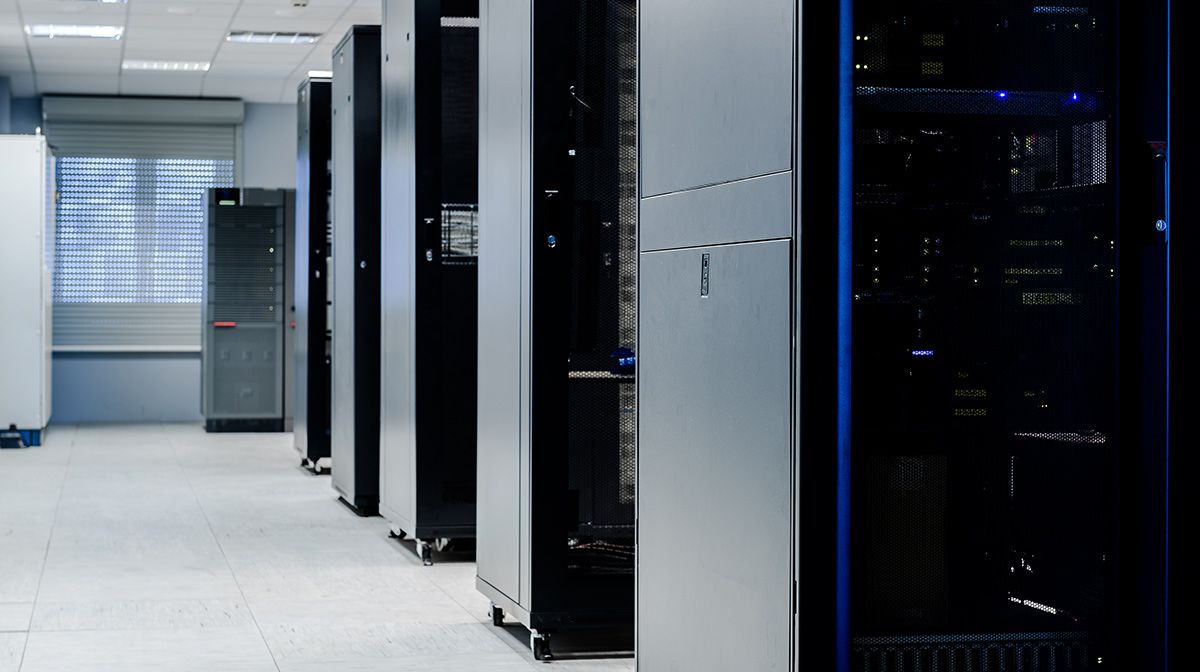
Computing & Media injection mold components Solution
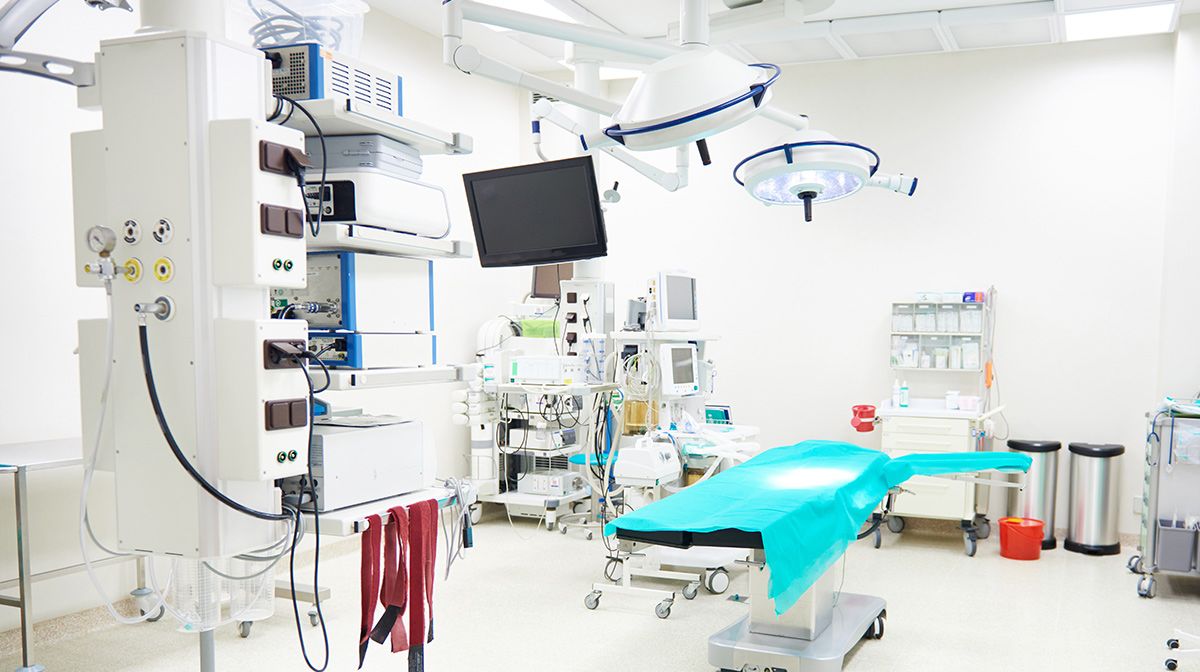